
SAP MRP vs. SAP CBP in SAP – Was sind die Unterschiede?
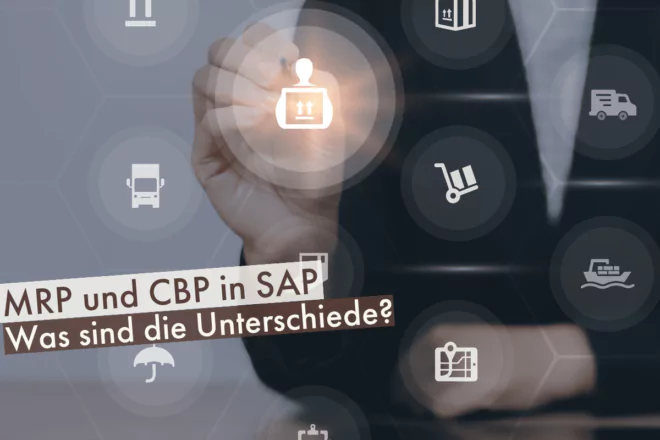
Sowohl die Materialbedarfsplanung (Material Requirement Planning – MRP) und die verbrauchsgesteuerte Disposition (Consumption Based Planning – CBP) sind zwei Arten der Beschaffungsplanung, die für eine optimale Verfügbarkeit von Materialien im Unternehmen sorgen sollen. Doch was unterscheidet die beiden Tools? Wir erklären Ihnen in diesem Beitrag die Unterschiede und Funktionsweisen von SAP MRP und CBP.
Was ist SAP MRP?
SAP MRP (Material Requirements Planning) ist ein Modul innerhalb des SAP-Systems, das Sie dabei unterstützt, Ihren Materialbedarf effizient zu planen und zu steuern. MRP ist ein wesentlicher Bestandteil des Supply Chain Managements und befasst sich mit der Optimierung des Bestandsmanagements, der Bedarfsplanung und der Beschaffung von Materialien.
Das SAP MRP-Modul ermöglicht es Ihnen, den Materialbedarf für Ihre Produktionsprozesse zu ermitteln und automatisch den Beschaffungsprozess auszulösen. Es berücksichtigt verschiedene Faktoren wie den aktuellen Lagerbestand, geplante Produktion, Kundenaufträge, Lieferzeiten, Beschaffungszeiten und andere Parameter, um den genauen Bedarf zu berechnen.
Die Hauptziele von SAP MRP sind die Optimierung der Bestände, die Reduzierung von Engpässen und die Sicherstellung einer kontinuierlichen Materialversorgung. Mit dem Modul können Sie den Materialfluss effizient planen, Überbestände vermeiden und gleichzeitig sicherstellen, dass die benötigten Materialien zum richtigen Zeitpunkt verfügbar sind.
SAP MRP bietet verschiedene Funktionen, darunter:
- Bedarfsermittlung: Es berechnet den Materialbedarf basierend auf verschiedenen Faktoren und erstellt eine Materialbedarfsliste.
- Beschaffungsplanung: Es plant die Beschaffung von Materialien, um den ermittelten Bedarf zu decken. Es berücksichtigt dabei Faktoren wie Lieferzeiten, Mindestbestände und Bestellmengen.
- Terminplanung: Es erstellt einen Zeitplan für die Beschaffung und Produktion von Materialien, um sicherzustellen, dass sie rechtzeitig verfügbar sind.
- Engpassmanagement: Es identifiziert Engpässe oder Materialknappheiten und unterstützt bei der Umplanung, um die Auswirkungen auf die Produktionsprozesse zu minimieren.
- Bestandskontrolle: Es überwacht den Lagerbestand und hilft dabei, Überbestände oder Engpässe zu vermeiden.
SAP MRP ist in der Regel eng mit anderen SAP-Modulen wie dem Materialwirtschaftsmodul (MM) und dem Produktionsplanungsmodul (PP) integriert, um einen nahtlosen Informationsfluss zwischen den verschiedenen Bereichen des Unternehmens sicherzustellen.
Was ist SAP CBP?
SAP Consumption-Based Planning (MM-CBP), bzw. die verbrauchsgesteuerte Disposition, ist eine Planungsart, die in SAP verwendet wird, um den Materialbedarf auf der Grundlage des Verbrauchsverhaltens zu ermitteln. Das Konzept von CBP basiert auf der Idee, dass der Materialbedarf aufgrund des tatsächlichen Verbrauchs oder der historischen Verbrauchsmuster prognostiziert werden kann. Dabei werden Informationen über den Verbrauch von Materialien und statistische Verfahren genutzt, um den Bedarf für die Zukunft zu planen.
Die Verfahren der verbrauchsgesteuerten Disposition sind ohne Bezug zum Produktionsplan, d. h. die Nettobedarfsrechnung wird hier nicht durch einen Primär- oder Sekundärbedarf angestoßen, sondern entweder durch die Unterschreitung eines festgelegten Bestellpunktes (Meldebestand) oder durch Prognosebedarfe, die aus Vergangenheitsverbräuchen errechnet wurden.
Es gibt verschiedene Arten von CBP-Verfahren in SAP, darunter:
- Reorder Point Planning (ROP): Bei diesem Verfahren wird ein bestimmter Bestandspunkt festgelegt, der den Auslösepunkt für eine Bestellung darstellt. Wenn der Lagerbestand diesen Punkt erreicht, wird eine Bestellung automatisch generiert, um den Bestand aufzufüllen.
- Forecast-Based Planning: Hier wird der Materialbedarf aufgrund von Prognosen und historischen Verbrauchsmustern ermittelt. Basierend auf den Prognosen werden Bestellungen generiert, um den prognostizierten Bedarf zu decken.
- Time-Phased Planning: Beim Time-Phased Planning wird der Materialbedarf über einen bestimmten Zeitraum hinweg geplant, normalerweise in Form von Zeitphasen (z. B. Wochen oder Monate). Der Bedarf wird basierend auf dem Verbrauchsmuster und anderen Parametern wie Sicherheitsbestand, Lieferzeiten usw. berechnet.
- Automatic Replenishment (ARun): Dieses Verfahren basiert auf Echtzeitdaten des Materialverbrauchs und löst automatisch Bestellungen aus, um den Materialbedarf aufrechtzuerhalten. Es berücksichtigt den aktuellen Lagerbestand, den Verbrauch und andere Faktoren, um den optimalen Zeitpunkt für die Materialbeschaffung zu bestimmen.
Was sind die Unterschiede von MRP und CBP?
Der Hauptunterschied sollte nun deutlich geworden sein und liegt in der Herangehensweise, aber nochmal zur Zusammenfassung: MRP funktioniert unter Berücksichtigung bestimmter Faktoren wie dem aktuellen Lagerbestand, der geplanten Produktion, Kundenaufträgen, Lieferzeiten, Beschaffungszeiten etc. Bei der verbrauchsgesteuerten Disposition wird der Bedarf anhand historischer Verbrauchsmuster und des tatsächlichen Verbrauchs prognostiziert.
Klassifizierungen
Um das ganze nochmal zu verdeutlichen, machen wir einen kurzen Exkurs in die ABC-Klassifizierung.
Die ABC-Analyse ermöglicht die Planung von Ereignissen und die Entscheidungsfindung auf Basis von grundlegenden Daten. Dabei werden die Objekte nach A, B und C klassifiziert und gewichtet, wobei eine höhere Gewichtung auf eine größere Bedeutung für das Unternehmen hinweist. Diese Analyse wird insbesondere bei der Beschaffung von Gütern und Rationalisierungsprojekten angewendet.
Bei der Beschaffungsplanung werden zunächst die durchschnittlichen Verbrauchswerte des Materials ermittelt. Anschließend wird der prozentuale Anteil des jeweiligen Materials am Gesamtwert berechnet und in die entsprechende Klasse einsortiert. Dabei werden bestimmte Grenzwerte festgelegt, die den Anteil in den jeweiligen Klassen widerspiegeln.
- Klasse A: Hochwertig/Umsatzstark (20 % des Materials = 80 % vom Gesamtwert)
- Klasse B: Mittelwertig/mittlere Umsatzstärke (30 % des Materials = 15 % vom Gesamtwert)
- Klasse C: Niedrigwertig/geringe Umsatzstärke (50 % des Materials = 5 % vom Gesamtwert)
Durch die Klassifizierung in A-B-C Klassen wird dem Material unterschiedliche Gewichtung zugeordnet. Dadurch erhalten Sie Informationen darüber, ob die Beschaffung wirtschaftlich vorteilhaft oder unvorteilhaft ist.
Generell kann man sagen, dass MRP für Klasse-A-Teile und CBP für B- und C-Teile und Betriebsstoffe durchgeführt wird.
Bedarfsrechnung und Sicherheitsbestände
Für MRP gilt hier: Die Nettobedarfsrechnung wird auf der Grundlage des geplanten und des genauen Bedarfs ausgelöst. Und da der Nettobedarf dem exakten Bedarf entspricht, ist nur ein geringer Sicherheitsbestand erforderlich.
Für CBP hingegen ist zu beachten: Die Berechnung des Nettobedarfs wird auf der Grundlage von Meldebeständen oder durch eine Bedarfsvorhersage ausgelöst, die aus den Verbrauchsdaten der Vergangenheit berechnet wird. Da der Nettobedarf nicht dem exakten Bedarf entspricht, brauchen Sie einen höheren Sicherheitsbestand, um eine Out-of-Stock-Situation zu vermeiden.
Fazit
Wir können also zusammenfassen, dass MRP und CBP nicht unbedingt gegensätzliche Konzepte sind, sondern einfach nur unterschiedliche Ansätze zur Planung des Materialbedarfs darstellen, welche Sie meist auch bei verschiedenen Anwendungsfällen nutzen können. In einigen Fällen können Sie sie theoretisch auch zusammen verwenden, um eine umfassendere Materialplanung zu ermöglichen, bei der sowohl berechnete Bedarfe als auch Verbrauchsmuster berücksichtigt werden.