
Materialbedarfsplanung
Inhaltsverzeichnis
- Begriffsabgrenzungen: MRP und CRP
- Unterschiede zwischen MRP I und MRP II
- Aufgaben der Materialbedarfsplanung
- Prozess der Materialbedarfsplanung
- Ziele der Materialbedarfsplanung
- Die unterschiedlichen Bedarfsarten
- Methoden der Materialbedarfsplanung
- Methoden zur Optimierung der Bestände
- Herausforderungen der Materialbedarfsplanung
- Zukunft der Materialbedarfsplanung
- Fazit
- FAQ
Begriffsabgrenzungen: MRP und CRP
Das Material Requirements Planning (MRP) ist ein Teilbereich eines ERPs, der sich auf die Planung und Verwaltung von Materialien konzentriert. ERP-Systeme (Enterprise Resource Planning) sind umfassende Softwarepakete, die eine Vielzahl von Unternehmensfunktionen wie Finanzen, Personalwesen, Fertigung und Betrieb abdecken.
Die Kapazitätsbedarfsplanung (CRP) hingegen ist eine Untergruppe der Materialbedarfsplanung, die sich speziell damit befasst, dass eine Organisation über ein angemessenes Niveau der Ressourcen zur Deckung der Kundennachfrage verfügt.
MRP und CRP sind beides integrale Bestandteile des ERP-Systems eines Unternehmens. Während sich MRP in erster Linie mit den benötigten Materialien für die Herstellung eines Produkts befasst, konzentriert sich CRP darauf, dass genügend Kapazitäten vorhanden sind, um die Nachfrage der Kunden nach dem Produkt zu decken.
Die CRP wird in der Regel verwendet, um einen Kapazitätsplan zu erstellen, der die Menge an Ressourcen festlegt, um die Kundennachfrage über einen bestimmten Zeitraum zu decken. Auf dieser Grundlage können Entscheidungen über Investitionen in neue Kapazitäten, z. B. Anlagen und Ausrüstung, getroffen werden.
Beides sind wichtige Bestandteile der Arbeitsabläufe in einem Unternehmen, werden aber nicht immer gemeinsam eingesetzt. In einigen Fällen kann ein Unternehmen je nach seinen spezifischen Bedürfnissen das eine oder das andere System verwenden oder sogar beide Systeme auf unterschiedliche Weise nutzen.
Unterschiede zwischen MRP I und MRP II
Die Materialbedarfsplanung (MRP I) ist die einfachste Form der Disposition und wird für die Bestandsplanung auf Ebene der Komponenten verwendet. Sie berechnet den Bedarf für einzelne Komponenten auf der Grundlage der Nachfrage nach Fertigerzeugnissen.
Die klaren Vorteile liegen in der Einfachheit und entsprechend geringeren Kosten. Auf der negativen Seite werden keine Kapazitätsbeschränkungen oder Losgrößen berücksichtigt, was zu einer Überproduktion und potenziellen Bestandsprobleme führen kann.
Das Manufacturing Resources Planning (MRP II) ist eine fortgeschrittene Form von MRP, bei der nicht nur der Bedarf an Fertigerzeugnissen, sondern auch der Produktionsplan berücksichtigt wird. Dies ermöglicht eine bessere Bestandsplanung und kann zur Vermeidung von Produktionsengpässen beitragen.
Im Vergleich zu MRP I liegt der Vorteil in dem höheren Detaillierungsgrad, denn es werden unter anderem finanzielle Berechnungen, Personalbedarfe oder Nachfrageprognosen einbezogen. Dieser Vorteil wird jedoch besonders für kleinere und mittelständische Unternehmen zur Herausforderung, denn die Einrichtung und Datenpflege ist dementsprechend komplizierter.
Aufgaben der Materialbedarfsplanung
Das System für die Materialbedarfsplanung ist so konzipiert, dass es folgende Hauptaufgaben in einer Organisation erfüllt:
- Vorhersage des zukünftigen Materialbedarfs
- Ermittlung des Bedarfs an Materialien und Komponenten
- Terminierung der Beschaffung oder Herstellung von Materialien und Komponenten
- Erstellung von Berichten für die Entscheidungsfindung des Managements
Eine weitere wichtige Aufgabe ist zudem die Führung einer Datenbank mit Informationen über die Produkte, Komponenten und Materialien des Unternehmens. Diese Informationen umfassen die Menge jedes Artikels, die zur Herstellung eines Produkts erforderlich ist, die Vorlaufzeit für die Beschaffung oder Produktion jedes Artikels und die aktuellen Lagerbestände jedes Artikels.
Prozess der Materialbedarfsplanung
Während der Materialbedarfsplanung wird nicht nur der Bedarf an bestimmten Materialien bestimmt, sondern auch deren Verfügbarkeit verfolgt. Es soll sichergestellt werden, dass die Materialien zu dem benötigten Zeitpunkt zur Verfügung stehen und Engpässe oder Überbestände vermieden werden.
Der MRP-Prozess beginnt mit der Entwicklung eines Produktionsplans (MPS). Dies ist ein Plan, der angibt, wann jedes Produkt in welcher Menge produziert wird. Der MPS berücksichtigt die verfügbare Kapazität der Herstellungs- oder Produktionsanlage sowie alle anderen Einschränkungen wie die Verfügbarkeit von Rohstoffen.
Sobald der MPS entwickelt wurde, erstellt das Dispositionssystem damit eine Liste des Materialbedarfs für jedes Bauteil oder Rohmaterial, das zur Herstellung der angegebenen Produkte benötigt wird. Das Dispositionssystem bestimmt anschließend auf der Grundlage der Vorlaufzeit für jede Komponente, wann diese Materialien bestellt und empfangen werden müssen. Die Vorlaufzeit ist der Zeitraum, der für die Beschaffung oder Herstellung einer Komponente erforderlich ist.
Das MRP-System überwacht ständig die Lagerbestände der einzelnen Komponenten und Rohstoffe. Wenn der Bestand eines bestimmten Artikels unter den Meldebestand fällt, wird ein Auftrag zur Auffüllung des Bestands erteilt. Die Bestellmenge wird durch die Losgröße für diesen Artikel bestimmt.
Der Prozess der Materialbedarfsplanung ist eine entscheidende Komponente des Herstellungsprozesses, denn Störungen oder Verzögerung können weitreichende Folgen für die Wirtschaftlichkeit haben.
Ziele der Materialbedarfsplanung
Die Ziele der Materialbedarfsplanung untergliedern sich in zwei Hauptziele.
Zum einen soll der korrekte Lagerbestand für die Produktionsplanung aufrechterhalten werden, wozu die richtigen Materialien bei Bedarf zur Verfügung stehen müssen.
Zum anderen sollen die Gesamtkosten des Lagerbestands minimiert werden. Um dies zu erreichen, werden Materialien nur dann gekauft, wenn sie benötigt werden, sodass keine überschüssigen Bestände entstehen. Dazu müssen potenzielle Produktionsengpässe erkannt und behoben werden, bevor sie Probleme verursachen.
Zu den untergeordneten Zielen zählen:
- die Minimierung der Anzahl der Bestandsposten,
- die Zeitreduzierung für die Materialbeschaffung,
- und die Verbesserung der Prognosegenauigkeit.
Die Ziele lassen sich teils schwer miteinander vereinbaren. Eine Verringerung der Anzahl der Bestandspositionen würde normalerweise zu einer Verlängerung der für die Materialbeschaffung benötigten Zeit führen. Gerade deswegen ist die Materialbedarfsplanung so wichtig, denn je besser der Prozess optimiert ist, desto mehr kann dieser Effekt minimiert werden.
Die unterschiedlichen Bedarfsarten
Grundsätzlich unterscheidet man in der Materialbedarfsplanung zwischen drei Bedarfsarten:
- Primärbedarf
- Sekundärbedarf
- Tertiärbedarf
Der primäre Bedarf besteht aus Waren, verkaufsfähigen Einheiten und Ersatzteilen. Auf der Grundlage des anfänglichen Bedarfs wird ein Produktionsplan erstellt. Dieser umfasst die Kapazitätsplanung, die Losgrößenplanung und die Bestandsplanung.
Der sekundäre Bedarf ergibt sich aus der Nachfrage an Rohstoffen, Komponenten und Baugruppen, die für die Produktion oder Herstellung des Primärbedarfs benötigt werden.
Der tertiäre Bedarf bezeichnet den Bedarf an Hilfs- und Betriebsstoffen, sowie Verschleißwerkzeugen, die für den Sekundärbedarf benötigt werden.
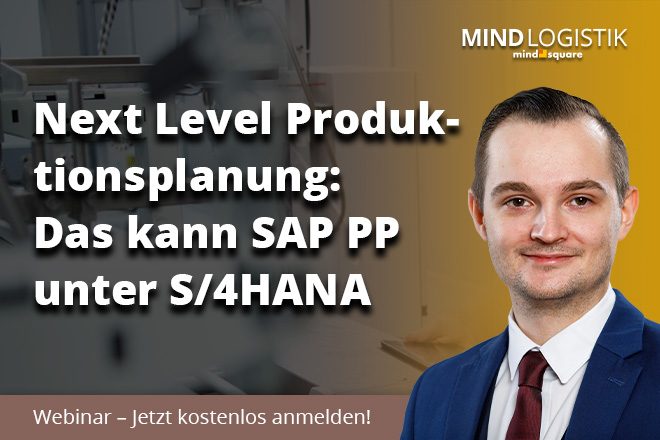
Methoden der Materialbedarfsplanung
Um die Planung möglichst effektiv zu gestalten, nutzen Unternehmen verschiedene Methoden zur Ermittlung des Bedarfs. Bei der Auswahl der geeigneten Methode müssen die Unternehmen Folgendes berücksichtigen:
- Grad der erforderlichen Detailplanung
- Höhe der Integration mit anderen Organisationssystemen
- Art des Fertigungsprozesses
- Höhe des Planungshorizonts
- Anzahl der Produkte und SKUs
Zu den am häufigsten eingesetzten Methoden zählen:
Die deterministische Bedarfsermittlung
Die deterministische Bedarfsplanung ist eine Methode der Materialbedarfsplanung, bei der feste mathematische oder statistische Modelle verwendet werden, um den künftigen Bedarf vorherzusagen. Dies ermöglicht eine genaue Planung für langfristige Vorhersagen, kann aber kurzfristig weniger effektiv sein, da plötzliche Änderungen der Nachfrage nicht berücksichtigt werden.
Die stochastische Bedarfsermittlung
Die stochastische Bedarfsplanung nutzt probabilistische Modelle zur Vorhersage des zukünftigen Bedarfs. Das bedeutet, dass bei der stochastischen Planung keine festen Modelle verwendet werden, sondern eine Reihe möglicher Werte, um die Nachfrage vorherzusagen. Dies ist kurzfristig effektiver als eine deterministische Planung, kann aber langfristig weniger genau sein.
Die heuristische Bedarfsermittlung
Die heuristische Bedarfsermittlung ist eine Technik der Materialbedarfsplanung, die auf Erfahrungswerten und Faustregeln beruht, um Entscheidungen über die Planung zu treffen. Sie ist weniger genau als andere Methoden, kann aber aufgrund ihrer Flexibilität kurzfristig effektiver sein.
Methoden zur Optimierung der Bestände
Eine ungenaue Bestandsführung bringt weitreichende Folgen mit sich. Ein zu hoher Bestand kann zu hohen Lagerkosten führen, während ein zu geringer Bestand zu Fehlbeständen und Umsatzeinbußen führen kann. Die Materialbedarfsplanung muss daher Folgende Punkte beachten:
- Wiederbestellungspunkte
- Sicherheitsbestand
- Vorlaufzeit
- Mindestbestellmenge
- Wirtschaftliche Bestellmengen
Um kostenintensive Fehler zu vermeiden, gibt es eine Reihe von Analysen und Instrumenten, die Unternehmen helfen, ihre Lagerbestände zu optimieren. Häufig werden die folgenden drei Grundverfahren für die Optimierung eingesetzt:
Die ABC-Analyse
Das ABC-Klassifizierungssystem ist eine Methode zur Kategorisierung von Beständen auf der Grundlage ihres Wertes. Die Artikel werden in drei Kategorien unterteilt:
- A-Positionen: hoher Wert, geringes Volumen
- B-Positionen: mittlerer Wert, mittleres Volumen
- C-Positionen: geringer Wert, hohes Volumen
Dieses System priorisiert die Ressourcen, um den Überblick über wichtige oder weniger wichtige Positionen zu behalten.
Die Materialflussanalyse (MFA)
Dies ist ein Instrument zur Veranschaulichung des Materialflusses, um potenzielle Engpässe und Ineffizienzen zu ermitteln. Man unterscheidet zwischen der qualitativen und der quantitativen Methode.
Die qualitative MFA wird zur Erstellung eines Materialflussdiagramms verwendet, das den Materialfluss im Unternehmen darstellt. Die quantitative Materialflussanalyse nutzt dann statistische Methoden, um die Materialflüsse zu quantifizieren.
Es ist eine leistungsfähige Methode zur Optimierung von Produktionsprozessen und der Verbesserung der Materialhandhabung.
Das Wertstrom-Mapping (VSM)
Hierbei handelt es sich um eine Methode zur Kartierung des Material- und Informationsflusses in einem Fertigungsprozess. VSM kann verwendet werden, um Engpässe und Ineffizienzen in Produktionsprozessen zu identifizieren.
Die Wertstromanalyse ist ein nützliches Instrument zur Prozessverbesserung und kann in Verbindung mit anderen Methoden, wie MFA und CRP, eingesetzt werden.
Herausforderungen der Materialbedarfsplanung
Die Materialbedarfsplanung kann ein komplexer und zeitaufwendiger Prozess sein und erfordert ein sorgfältiges Management. Besonders für Unternehmen, die Produkte mit langen Vorlaufzeiten herstellen oder mit häufigen Nachfrageschwankungen konfrontiert sind, ist diese Planung jedoch unerlässlich.
Die größte Herausforderung ist die genaue Vorhersage des künftigen Bedarfs. MRP wurde für eine einfachere Zeit entwickelt, als die Lieferkette kürzer und weniger komplex war. Heute sind Lieferketten oft global und vielseitig gestaltet, mit vielen verschiedenen Lieferanten und Produkten.
Diese Komplexität macht es schwierig, die Nachfrage genau vorherzusagen und die Produktion zu planen. Wenn die Vorhersage ungenau ist, kann dies zu Materialmangel oder -überschüssen führen, was die Produktion stören oder die Kosten erhöhen kann.
Zudem kommt die Sicherstellung der rechtzeitigen Lieferungen und der Umgang mit Unterbrechungen in der Lieferkette. Lieferstörungen durch externe Ereignisse wie Naturkatastrophen, politische Instabilität oder, wie zuletzt, durch Pandemien, können nicht eingeplant werden. Selbst bei bester Planung führen diese Störungen zu kostspieligen Verzögerungen. Anschließend liegt es an der Materialbedarfsplanung, diese Unterbrechungen schnellstmöglich zu lösen.
Eine weitere Herausforderung ist die Ressourcenintensität, sowohl in Bezug auf die Zeit, die für die Durchführung von MRP-Berechnungen benötigt wird, als auch die IT-Infrastruktur, die zur Unterstützung erforderlich ist.
Das größte Werkzeug, um diese Herausforderungen zu meistern, sind daher die Materialbedarfsplanungssysteme. Sie unterstützen Unternehmen in der Erstellung genauer Bedarfsprognosen, optimierten Produktionspläne und verbesserten Lagerbeständen.
Zukunft der Materialbedarfsplanung
Die Zukunft der Materialbedarfsplanung wird sich wahrscheinlich von den Verfahren unterscheiden, die seit vielen Jahren angewandt werden. Die wichtigsten Triebkräfte des Wandels sind neue Technologien, die Lieferketten vereinfachen und die Vorhersage der künftigen Nachfrage erleichtern.
Diese Veränderungen werden tiefgreifende Auswirkungen auf die Arbeitsweise der Unternehmen und die Verwaltung ihrer Lieferketten haben. Die Materialbedarfsplanung wird weiterhin ein wichtiges Instrument sein, aber die Prozesse und Systeme, die sie unterstützen, werden vermutlich sehr unterschiedlich sein.
Die Fortschritte der eingesetzten Software verbessern beispielsweise die Vorhersagegenauigkeit erheblich. So kann etwa das Internet der Dinge und Künstliche Intelligenz genutzt werden, um Lagerbestände zu verfolgen und die künftige Nachfrage vorherzusagen.
Das Cloud Computing unterstützt und vereinfacht den Informationsaustausch zwischen den unterschiedlichen Teilen der Lieferkette. Dies erleichtert die Koordinierung der verschiedenen Aspekte der Produktion und stellt sicher, dass die es weder zu Engpässen noch zu überfüllten Lagern kommt.
Eines der am meisten eingesetzten Softwaresysteme für die Materialbedarfsplanung ist SAP MM. Das Tool ermöglicht zusätzlich eine mobile Datenerfassung und lässt Nutzer ihre Lagerbestände verwalten, künftige Nachfragen vorhersagen und Berichte erstellen.
Trotz der schnellen Fortschritte der Technologie wird es einige Zeit dauern, bis die Unternehmen ihre Materialbedarfsplanungsprozesse anpassen, um alle Vorteile zu nutzen. Die Unternehmen, die sich rechtzeitig anpassen, werden jedoch gut positioniert sein, um in Zukunft im Wettbewerb bestehen zu können.
Fazit
Die Materialbedarfsplanung (MRP) ist ein Produktionsplanungs-, Terminierungs- und Bestandskontrollsystem, das für die Verwaltung von Fertigungsprozessen eingesetzt wird. Sie ist daher ein bedeutsamer Baustein des Lieferkettenmanagements.
MRP hat zwar seine Grenzen, ist dennoch ein wertvolles Instrument zur Optimierung von Produktion und Lagerbeständen. Je besser Unternehmen ihren Materialplanungsprozess verstehen, desto effektiver können sie MRP nutzen, um ihre Abläufe zu rationalisieren und somit ihre allgemeine Wettbewerbsfähigkeit zu verbessern.
FAQ
Was ist Materialbedarfsplanung?
Die Materialbedarfsplanung ist ein Systemansatz zur Verwaltung von Materialien und Bauteilen in Fertigungsunternehmen. Sie hilft den Produktionsplanern, die Mengen an Materialien zu bestimmen, die das Unternehmen bestellen und produzieren muss, um den zukünftigen Bedarf zu decken.
Wie funktioniert MRP?
Das Material Requirements Planning (MRP) ist ein Teilbereich eines ERP-Systems, das sich auf die Planung und Verwaltung von Materialien konzentriert. Dabei nutzt das MRP Informationen aus einer Liste von Materialien (Bill of Materials, BOM), den vorhandenen Materialien im Lager und dem Produktionsplan, um zu berechnen, welche Materialien die Produktion wann benötigt.
Was sind die Aufgaben der Materialbedarfsplanung?
Die Materialbedarfsplanung hat mehrere Hauptaufgaben. Darunter fallen die Vorhersage des zukünftigen Materialbedarfs, die Ermittlung des Bedarfs an Materialien und Komponenten, die Terminierung der Beschaffung oder Herstellung von Materialien und Komponenten sowie die Erstellung von Berichten für die Entscheidungsfindung des Managements.
Wenn Sie weitere Fragen zur Materialbedarfsplanung haben, dann nehmen Sie gerne zu uns Kontakt auf.
Wer kann mir beim Thema Materialbedarfsplanung helfen?
Wenn Sie Unterstützung zum Thema Materialbedarfsplanung benötigen, stehen Ihnen die Experten von Mindlogistik, dem auf dieses Thema spezialisierten Team der mindsquare AG, zur Verfügung. Unsere Berater helfen Ihnen, Ihre Fragen zu beantworten, das passende Tool für Ihr Unternehmen zu finden und es optimal einzusetzen. Vereinbaren Sie gern ein unverbindliches Beratungsgespräch, um Ihre spezifischen Anforderungen zu besprechen.