
Lean Production
Inhaltsverzeichnis
Definition und Historie
Der Begriff Lean Production, auch Lean Manufacturing, bezeichnet ursprünglich eine systematisierte Organisation der Fertigung. Seine Ursprünge hat das Konzept beim japanischen Automobilhersteller Toyota, wo es bereits in den 1950er Jahren erstmalig zur Anwendung kam. Es ist einer von mehreren Teilbereichen des sogenannten Lean Managements – einer Unternehmensphilosophie des Weglassens aller überflüssigen Tätigkeiten in Verwaltung und Produktion.
Für die Fertigung bedeutet dies, dass sämtliche Produktionsfaktoren (bis ins Kleinste) kontinuierlich auf Einsparungs- und Optimierungsmöglichkeiten untersucht werden. Insbesondere Überproduktion, fehlerhafte Produkte und lange Durchlaufzeiten sollen vermieden werden. In Kombination mit der schlanken Verwaltung (Lean Administration) halbieren Unternehmen idealerweise ihre Kosten, während sie ihre Produktivität verdoppeln.
Lean Production beinhaltet außerdem eine straffere Koordination der Zulieferer, eine Flexibilisierung der Produktionsprozesse sowie eine Reorganisation der Fertigungsabläufe.
Ziele
Die Ziele der Lean Production lassen sich folgendermaßen zusammenfassen:
- Optimale Produktivität der Produktionsfaktoren erreichen
- Hohe Produktqualität sicherstellen
- Hoch flexible Produktionsumgebung realisieren
- Produktionszeit senken
- Verschwendung reduzieren
- Ressourcen effizient einsetzen
- Kosten minimieren
Gründe für Lean Production
Unternehmen sehen sich heute einem hohen, internationalen Wettbewerbsdruck ausgesetzt. Die Lebenszyklen von Produkten werden immer kürzer. Gleichzeitig steigen die Kundenanforderungen in puncto Individualität, Vielfalt und Qualität. Um in diesem Szenario weiterhin konkurrenzfähig zu bleiben, müssen Unternehmen mehrere Ziele verfolgen:
- Flexibel auf Kundenwünsche eingehen
- Produktvielfalt anbieten
- Hohe Produktqualität sicherstellen
- Produktverfügbarkeit gewährleisten
- Neue Produkte regelmäßig und schnell in den Markt bringen
Gleichzeitig besteht jedoch ein hoher Kostendruck. Daher ist es notwendig, die Prozesse nicht nur zu flexibilisieren, sondern auch zu verschlanken. An dieser Stelle kommt die Lean-Production-Philosophie ins Spiel. Sie hilft Unternehmen dabei, Ressourcen in der Produktion effizient einzusetzen und Verschwendung in sämtlichen Bereichen zu minimieren. In Summe sorgt das Konzept also dafür, dass Unternehmen trotz steigender Kundenanforderungen und hohem Wettbewerbsdruck weiterhin wirtschaftlich agieren können.
Vor- und Nachteile von Lean Production
Lean Production hat zahlreiche Vorzüge für Unternehmen. So können Betriebe schneller produzieren, Fabrikflächen einsparen, unproduktive Personalressourcen abbauen und Lagerbestände deutlich senken. Ebenso lassen sich Fehlerquellen in der Fertigung identifizieren und minimieren. Gleichzeitig trägt die schlanke Produktion dazu bei, Belieferungszeiten zu reduzieren. Dies führt zu einer höheren Kundenzufriedenheit.
Dem gegenüber hat Lean Production auch einige Nachteile und Risiken. So lassen sich kurzfristige Störungen im Nachschub aufgrund der knappen Lagerbestände kaum abfedern. Weiterhin ist die Just-in-time-Produktion, welche mit der schlanken Produktion einhergeht, im Hinblick auf die Nachhaltigkeit fragwürdig. Sie erfordert nämlich viele kleinere Materiallieferungen, die erhöhte CO2-Emissionen verursachen. Auch hinsichtlich der jüngsten weltweiten Krisen und Lieferkettenprobleme sind minimale Materialbestände ein Problem. Ein weiterer Nachteil besteht darin, dass Lean Manufacturing standardmäßig auf eine begrenzte Produktvielfalt abzielt. Dies widerspricht dem aktuellen Trend der steigenden Variantenanzahl.
Konzept: Die drei Säulen der Lean Production
Das Konzept der Lean Production besteht aus drei Säulen:
- Steigerung der Produktivität
- Steigerung der Produktqualität
- Steigerung der Flexibilität
1. Säule: Steigerung der Produktivität
Der Einsatz von Produktionsfaktoren soll bei gleichbleibendem Output reduziert werden. Hierzu senken Unternehmen ihre Lagerbestände. Sie verkürzen zudem die Durchlaufzeiten in der Fertigung und bauen ihre nicht ausgelasteten Kapazitäten ab. Als Ersatz für die bisherige Fertigungsorganisation wird Just-in-time eingeführt. Weitere Maßnahmen sind die Einführung flexibler Arbeitszeiten sowie der Abbau von Hierarchie-Ebenen, um eine effektivere Entscheidungsfindung zur realisieren.
2. Säule: Steigerung der Produktqualität
Mit der zweiten Säule der Lean Production steigern Unternehmen die Qualität ihrer Produkte. Hierfür werden regelmäßige, frühzeitig beginnende Qualitätskontrollen eingeführt. Defekte Produkte lassen sich dadurch sofort nachbearbeiten, wodurch sich der Ausschuss in der Produktion reduziert. Weiterhin soll die Produktqualität bereits in der Produktentwicklung laufend kontrolliert werden. Ebenso ist es das Ziel, die Zusammenarbeit mit den Lieferanten im Hinblick auf die Materialqualität zu verbessern.
3. Säule: Steigerung der Flexibilität
Das Ziel dieses Bausteins ist es, unterschiedliche Produktvarianten und -stückzahlen sowohl kostengünstig als auch zeitsparend herzustellen. Hierzu werden flexible Arbeitszeitmodelle und Produktionssysteme implementiert.
Gestaltungsprinzipien der Lean Production
Produktionssysteme können nur dann erfolgreich sein, wenn sie insgesamt auf den Kundennutzen ausgerichtet sind. In Deutschland hat sich diese Erkenntnis in dem Begriff „Ganzheitliche Produktionssysteme“ (GPS) manifestiert. GPS nutzen die Methoden von Lean Production, wobei sich acht verschiedene Gestaltungsprinzipien unterscheiden lassen:
1. Vermeidung von Verschwendung (Muda)
In der Lean-Philosophie ist Verschwendung (Muda) das Gegenstück zu Wert. Daher ist es das Ziel, den Wert zu erhöhen und Verschwendung zu vermeiden. Alle Produktionsfaktoren, die nicht zur Wertsteigerung beitragen, müssen minimiert werden. Darüber hinaus müssen Prozesse so organisiert werden, dass sie ressourceneffizient sind, die Verschwendung reduzieren und die Durchlaufzeiten verkürzen (weitere Details im Abschnitt „Formen der Verschwendung“). Die Minimierung der Ressourcenverschwendung verbessert im Übrigen auch die Nachhaltigkeit des Wirtschaftens. Somit hat Lean Production in diesem Punkt einen gesamtgesellschaftlichen Mehrwert.
2. Kontinuierlicher Verbesserungsprozess (Kaizen)
Ganzheitliche Produktionssysteme streben nach Perfektion. Um dieses Ziel zu erreichen, müssen bestehende Prozesse und Systeme fortlaufend verbessert werden. Hierbei ist es notwendig, die Mitarbeiter in den kontinuierlichen Verbesserungsprozess (KVP) mit einzubeziehen. Das heißt: Jeder einzelne Mitarbeiter muss Methoden, Abläufe und Werkzeuge stetig hinterfragen, um Optimierungen zu erzielen. Klassisch wird dies mit einem betrieblichen Vorschlagswesen oder Ideenmanagement gelöst.
3. Standardisierung
Die Standardisierung hat das Ziel, Handlungsschritte von sich wiederholenden Arbeitsabläufen, Fertigungsschritten, Prozessen sowie von Gestaltungs- und Planungsaufgaben festzulegen. Maßgabe ist es hierbei, stabilere Prozesse zu realisieren und nicht-wertschöpfende Tätigkeiten zu beseitigen.
4. Null-Fehler-Prinzip
Das Null-Fehler-Prinzip verhindert eine Weitergabe von Fehlern in die jeweils nächste Prozesseinheit. Zu diesem Zweck werden Qualitätskontrollen in die standardisierten Prozesse implementiert. Weiterhin enthält dieses Gestaltungsprinzip Methoden der Fehlervermeidung innerhalb von Prozessketten.
5. Fließprinzip
Dieses Prinzip hat das Ziel, einen reibungslosen Informations- und Materialfluss zu realisieren. Dadurch sinkt die Durchlaufzeit über die gesamte Wertschöpfungskette. Unter anderem werden Produkte beim Fließprinzip ohne Zwischenlagerung von einer Fertigungsstation zur nächsten transportiert.
6. Pull-Prinzip
Das Pull-Prinzip besagt, dass sich die Produktion an konkreten Kundenaufträgen orientiert. Der Kundenauftrag wird sozusagen durch den Fertigungsprozess „gezogen“. Das Gegenstück ist das Push-Prinzip („schieben“), wobei auf Basis prognostizierter Kundenbedarfe produziert wird. Mit dem Pull-Prinzip ist es möglich, Bestände zu minimieren und den Steuerungsaufwand in der Fertigung zu senken. Oft wird dieses Gestaltungsprinzip in Kombination mit Methoden wie Kanban, Just-in-time oder Just-in-sequence verwendet.
7. Lean Leadership
Der Begriff „Lean Leadership“ bezeichnet die zielorientierte Führung und Mitarbeiterorientierung eines Unternehmens. Mitarbeiter werden hierbei als wichtige Ressourcen für die kontinuierliche Prozessverbesserung und innovative Konzepte betrachtet. Die fehler- und verschwendungsfreie Arbeitsweise steht im Vordergrund. Sowohl Mitarbeiter als auch Führungskräfte profitieren zudem von einer zielorientierten Führung, die klar definierten Vorgaben folgt. Charakteristisch für Lean Leadership sind außerdem flache Hierarchien mit hoher Informationstransparenz.
8. Visuelles Management
Visuelles Management bedeutet, Informationen über die Produktion und ihre Prozesse bildlich darzustellen. Durch diese Maßnahme sollen die Ziele, Prozesse und Leistungen im Produktionssystem in hohem Maße transparent werden. Mitarbeiter und Führungskräfte haben jederzeit einen Einblick in Produktionskennzahlen. Daraus resultiert eine stärkere Identifikation mit dem Arbeitgeber und den eigenen Aufgaben. Ebenso lassen sich Zielabweichungen und Probleme schnell erkennen, sodass kurzfristige Gegenmaßnahmen abgeleitet werden können. Dies wiederum unterstützt die kontinuierliche Verbesserung und die Reduzierung von Verschwendung.
Lean Production: Beispiel
Wie Lean Production in der Praxis umgesetzt wird, zeigt unter anderem das Beispiel Toyota. Das Unternehmen sah sich aufgrund von Rohstoffknappheit, Sparmaßnahmen und Isolationspolitik dazu gezwungen, eine Just-in-time-Produktion einzuführen. Mit dem „Toyota-Produktionssystem“ (TPS) sollten größtmögliche Stückzahlen, bestmögliche Produktqualität und zudem pünktliche Auslieferungen erreicht werden. Um dies zu realisieren, setzt Toyota auf folgende Bausteine:
- Just-in-time: minimale Bestände
- Kanban und Pull-Prinzip: Herstellungsprozess wird ausgehend von einem Auftragseingang gesteuert
- Kaizen: fortlaufender Verbesserungsprozess unter Einbeziehung von Mitarbeitervorschlägen
Formen der Verschwendung
Ein Kernelement der Lean-Philosophie ist es, Verschwendung aufzufinden und zu eliminieren. Zur „Verschwendung“ zählt grundsätzlich alles, was keinen unmittelbaren Beitrag zur Wertschöpfung leistet. Oder aus Kundensicht formuliert: Verschwendung umfasst alle Aufwände, für die der Kunde nicht bereit wäre, zu zahlen. Daraus resultiert folgende Klassifikation von Prozessen:
- Kernprozesse: schaffen unmittelbare Wertschöpfung (unmittelbaren Kundennutzen)
- Unterstützungsprozesse: sind notwendig zur Durchführung der Kernprozesse
- Blindprozesse: haben keinen Kundennutzen, verursachen aber dennoch Aufwand
- Fehlprozesse: vernichten einen bereits realisierten Kundennutzen wieder
Im Sinne von Lean Production sind die ersten beiden Prozessarten möglichst gut zu organisieren, die letzten beiden hingegen möglichst zu eliminieren.
Die klassische Lean-Production-Lehre unterscheidet außerdem folgende Formen der Verschwendung, die es zu vermeiden gilt:
- Überproduktion (Over-Production): Produkte, Leistungen und Halbfabrikate, die ohne konkreten Kundenauftrag hergestellt werden.
- Bestände (Inventory): Zu hohe Bestände binden Kapital und Flächen. Sie generieren außerdem unnötigen Arbeitsaufwand. Teils müssen sie sogar entsorgt und abgeschrieben werden.
- Transport: Interne Materialprozesse erhöhen den Kundennutzen eines Produkts nicht. Einlagerungsprozesse werden in der Regel sogar als Blindprozesse betrachtet.
- Wartezeit (Waiting): Durch unterbrochene oder stockende Abläufe, Störungen von Maschinen, Probleme mit Betriebsmitteln, fehlendes Material und ähnliche Faktoren werden Ressourcen gebunden. Diese können dann vorübergehend nicht mehr wertschöpfend eingesetzt werden.
- Aufwendige Prozesse (Over-Engineering): Abläufe sind durch ungeeignete Systeme, Technologien und unzureichende Einbeziehung der Fertigung in die Produktentwicklung meist schwer zu kontrollieren. Dadurch entstehen Fehler und unproduktive Zeiten. Ebenso sinkt die Flexibilität.
- Lange Wege (Motion): Zu lange Wege stören den flüssigen Ablauf der Produktion.
- Fehler (Defects): Mangelhafte Produkte verursachen Korrekturaufwände (Blindprozesse) und Ausschuss (Fehlprozesse). Ebenso werden Prozesse unterbrochen und müssen neu gestartet werden (Blindprozesse).
- Ungenutztes Potenzial: Auch Knowhow und Fähigkeiten der Mitarbeiter, die nicht zur Verbesserung des Gesamtprozesses genutzt wird, gelten als Verschwendung.
Wichtige Kennzahlen
Inwiefern die Lean Production erfolgreich umgesetzt wird, lässt sich mit Kennzahlen überwachen. Teils führt deren reine Implementierung bereits zu ersten Verbesserungen. Wichtig sind vor allem folgende Indikatoren:
- Durchlaufzeit: Zeitspanne, die zur Herstellung von Produkten benötigt wird
- Fließgrad: Verhältnis von Bearbeitungszeit eines Produkts zur Durchlaufzeit
- Flusszahl: Anteil der Transport- oder Wartezeiten im Verhältnis zur reinen Bearbeitungszeit
- Wertschöpfungsgrad: Verhältnis von Wertschöpfung zu Gesamtleistung
- OEE (Overall equipment effectiveness): Gesamtanlageneffektivität
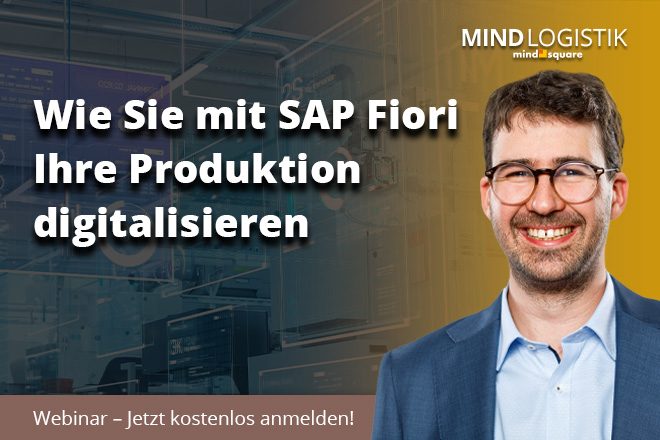
Voraussetzungen für Lean Production
Um die Produktion mithilfe von Lean Manufacturing zu optimieren, müssen zunächst alle Kostentreiber identifiziert werden. Diese grundlegende Analyse ist die Basis für alle weiteren Verbesserungsmaßnahmen. Die zweite wichtige Voraussetzung besteht darin, dass alle Produktionsprozesse standardisiert und in hohem Maße optimiert werden. Erreichbar ist dies durch eine Kombination mehrerer Managementkonzepte. Standardisierung reicht jedoch nicht aus. Lean Production erfordert außerdem die Entwicklung neuer, effizienterer Fertigungsprozesse.
Fazit
In Summe lassen sich mit Lean Production zahlreiche Verbesserungen erzielen. Die Bandbreite reicht von kürzeren Durchlaufzeiten über geringere Bestände bis hin zu höherer Produktivität. Dennoch schrecken einige Unternehmen in Deutschland davor zurück, das Konzept in Gänze zu implementieren. Oft scheitern entsprechende Initiativen an der Einbeziehung von Mitarbeitern und Lieferanten. Doch auch der notwendige Kulturwandel ist eine enorme Herausforderung.
Reduzieren lassen sich die Einstiegshürden mittlerweile jedoch durch verschiedene digitale Technologien. Diese bieten hohes Potenzial, Fertigungsprozesse (weiter) zu verschlanken. Vor allen Dingen spielen Sensortechnologien und die Echtzeit-Produktionsüberwachung dabei eine wesentliche Rolle. Wichtig sind jedoch auch Big-Data-Analysen, da sie die Möglichkeit bieten, Bedarfe und Nachschublieferungen zu prognostizieren, die Produktionsplanung zu unterstützen und Verbesserungspotenziale in den Abläufen aufzudecken.
FAQ
Wie funktioniert Lean Production?
Lean Production ist eine Methode des Lean Managements, die Unternehmen dabei unterstützt, Personal, Material, Betriebsmittel, Planung und Organisation sparsam und zeiteffizient einzusetzen. Sie zielt darauf ab, flache Hierarchien zu schaffen, Kosten zu senken und die Produktivität zu steigern, während gleichzeitig die Produktqualität und Prozessflexibilität erhöht werden sollen.
Was sind die Ziele der Lean Production?
Die Ziele der Lean Production umfassen, eine optimale Produktivität der Produktionsfaktoren zu erreichen, eine hohe Produktqualität sicherzustellen, hoch flexible Produktionsumgebungen zu realisieren, Produktionszeit zu senken, Verschwendung zu reduzieren, Ressourcen effizient einzusetzen und Kosten zu minimieren.
Warum setzen Unternehmen Lean Production ein?
Unternehmen setzen Lean Production ein, um im heutigen internationalen Wettbewerbsumfeld konkurrenzfähig zu bleiben. Lean Production ermöglicht es ihnen, flexibel auf Kundenwünsche einzugehen, eine Vielzahl von Produkten anzubieten, hohe Produktqualität sicherzustellen, Produktverfügbarkeit zu gewährleisten und neue Produkte schnell auf den Markt zu bringen. Gleichzeitig hilft Lean Production, Kosten zu senken und Ressourcen effizient einzusetzen.
Haben Sie weitere Fragen zur Lean Production? Dann nehmen Sie gerne zu uns Kontakt auf.
Wer kann mir beim Thema Lean Production helfen?
Wenn Sie Unterstützung zum Thema Lean Production benötigen, stehen Ihnen die Experten von Mindlogistik, dem auf dieses Thema spezialisierten Team der mindsquare AG, zur Verfügung. Unsere Berater helfen Ihnen, Ihre Fragen zu beantworten, das passende Tool für Ihr Unternehmen zu finden und es optimal einzusetzen. Vereinbaren Sie gern ein unverbindliches Beratungsgespräch, um Ihre spezifischen Anforderungen zu besprechen.